Semiconductor Application: Bagong ULVAC System
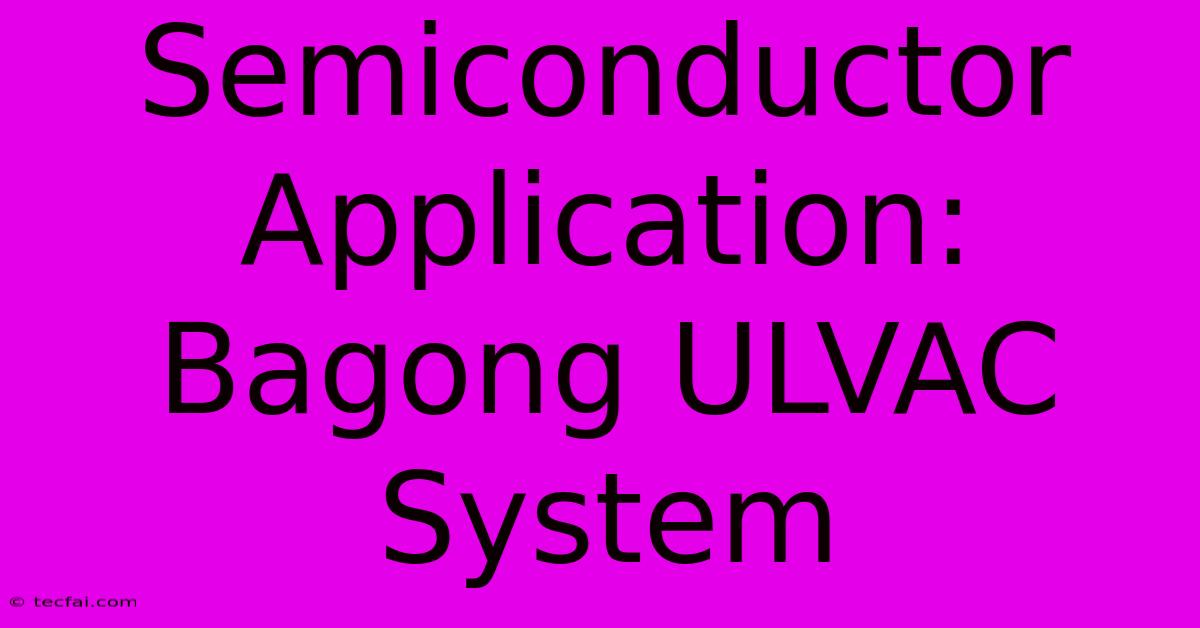
Discover more detailed and exciting information on our website. Click the link below to start your adventure: Visit Best Website tecfai.com. Don't miss out!
Table of Contents
Semiconductor Application: The Novel ULVAC System
The semiconductor industry is constantly evolving, demanding innovative solutions for increasingly complex manufacturing processes. One area experiencing significant advancements is vacuum technology, crucial for various stages of chip production. This article delves into the application of a novel ULVAC system within the semiconductor industry, highlighting its key features and advantages. We'll explore its impact on efficiency, precision, and overall yield in semiconductor fabrication.
Understanding the Need for Advanced Vacuum Systems in Semiconductor Manufacturing
Semiconductor manufacturing relies heavily on vacuum environments to prevent contamination and ensure the precise deposition and etching of materials. Traditional vacuum systems often face limitations in achieving the ultra-high vacuum (UHV) levels and precise control necessary for advanced node fabrication. This is where the innovative ULVAC system comes into play.
The Novel ULVAC System: A Technological Leap Forward
This cutting-edge system represents a significant advancement in vacuum technology, offering several key improvements over its predecessors:
-
Enhanced Vacuum Performance: The system boasts significantly improved UHV capabilities, achieving lower ultimate pressures and faster pump-down times. This is crucial for minimizing particle contamination and ensuring the integrity of delicate semiconductor structures.
-
Precise Process Control: The system offers superior control over process parameters, including pressure, temperature, and gas flow. This level of precision is essential for creating consistent and high-quality semiconductor devices. Real-time monitoring and advanced control algorithms contribute to this accuracy.
-
Reduced Downtime: Its robust design and advanced diagnostics minimize downtime associated with maintenance and repairs, leading to increased productivity and lower operational costs. Predictive maintenance capabilities further enhance uptime.
-
Improved Material Handling: The system incorporates advanced material handling mechanisms, reducing the risk of contamination and ensuring efficient processing of wafers. This includes features designed to minimize vibration and protect delicate semiconductor materials.
-
Scalability and Flexibility: The system’s modular design allows for easy scalability to accommodate different production volumes and process requirements. This adaptability makes it suitable for a range of semiconductor manufacturing applications.
Specific Applications within Semiconductor Fabrication
This advanced ULVAC system finds application in several critical semiconductor processes:
-
Thin Film Deposition: The precise control and ultra-high vacuum capabilities are crucial for achieving high-quality thin film deposition, essential for creating various semiconductor components.
-
Etching Processes: The system's ability to maintain precise pressure and gas flow is essential for controlled etching processes, ensuring accurate removal of materials without damaging the underlying substrate.
-
Surface Treatment: Preparing the wafer surface for subsequent processes requires a clean, controlled environment, which this ULVAC system effectively provides.
-
Packaging and Sealing: Maintaining a high-vacuum environment during packaging is crucial for protecting sensitive semiconductor devices from atmospheric contamination.
Competitive Advantages and Future Outlook
Compared to traditional vacuum systems, this novel ULVAC system offers several advantages, including:
-
Higher Throughput: Faster pump-down times and reduced downtime directly translate to higher throughput and improved production efficiency.
-
Improved Yield: The enhanced precision and reduced contamination risk lead to significantly improved yield rates, minimizing waste and maximizing profitability.
-
Lower Operating Costs: Reduced maintenance, longer operational lifespan, and higher yields contribute to lower overall operating costs.
The future of this technology looks promising. Ongoing research and development efforts will likely lead to further advancements in vacuum performance, process control, and overall system efficiency. This continued innovation will be crucial in supporting the continued miniaturization and performance enhancements of semiconductor devices. The ULVAC system is poised to play a vital role in enabling the next generation of semiconductor manufacturing.
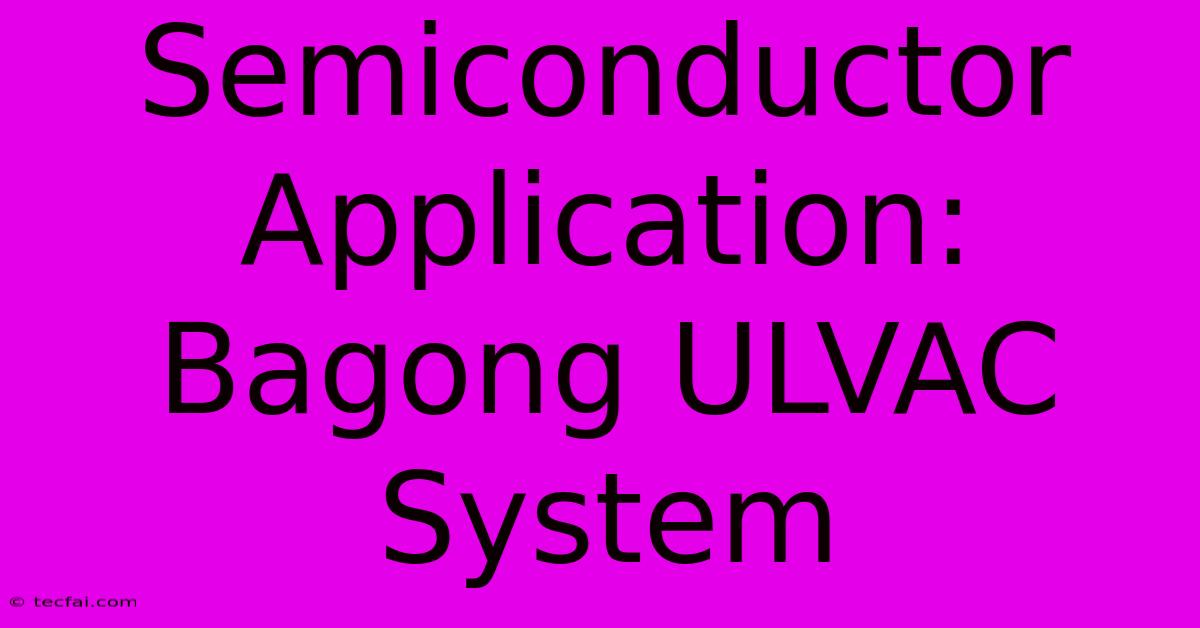
Thank you for visiting our website wich cover about Semiconductor Application: Bagong ULVAC System. We hope the information provided has been useful to you. Feel free to contact us if you have any questions or need further assistance. See you next time and dont miss to bookmark.
Featured Posts
-
Entron Exx Deposition System Ng Ulvac
Dec 03, 2024
-
Dental Treatment Delay Womans Extreme Action
Dec 03, 2024
-
Government Accused Of Recession Delay
Dec 03, 2024
-
Nhs Dentist Wait 7 Years 3 Teeth Extracted
Dec 03, 2024
-
Price Rejects 2025 Premier League Darts Spot
Dec 03, 2024