ENTRON-EXX: Deposition System Ng ULVAC
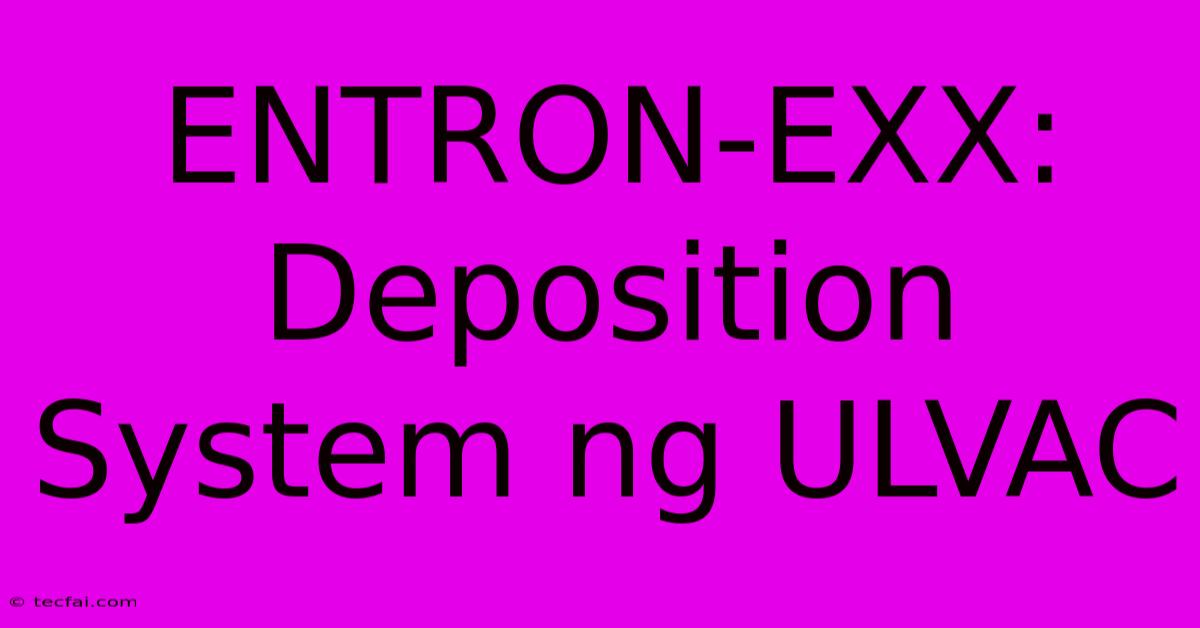
Discover more detailed and exciting information on our website. Click the link below to start your adventure: Visit Best Website tecfai.com. Don't miss out!
Table of Contents
ENTRON-EXX: ULVAC's Cutting-Edge Deposition System
ULVAC's ENTRON-EXX represents a significant advancement in thin-film deposition technology. This sophisticated system offers unparalleled precision and control, making it a valuable tool for researchers and manufacturers alike in various industries. Let's delve deeper into its capabilities and explore why it's leading the pack in deposition system innovation.
Understanding the Need for Advanced Deposition Systems
Before diving into the specifics of the ENTRON-EXX, it's crucial to understand the importance of precise thin-film deposition. This process is fundamental to the creation of numerous advanced technologies, including:
- Semiconductors: The creation of microchips relies heavily on the precise deposition of various materials onto silicon wafers.
- Optics: High-quality optical components, such as lenses and filters, require extremely accurate thin-film coatings.
- Solar Cells: Efficient solar cells depend on the precise deposition of light-absorbing materials.
- Displays: The vibrant colors and clarity of modern displays are achieved through sophisticated thin-film technologies.
The ENTRON-EXX addresses the growing demand for higher precision, greater throughput, and improved control in these and other applications.
Key Features of the ENTRON-EXX Deposition System
ULVAC's ENTRON-EXX boasts several key features that set it apart from competing systems:
- High-Precision Deposition: The system utilizes advanced techniques to ensure extremely precise control over film thickness and uniformity, resulting in superior product quality. This precision is crucial for applications requiring tight tolerances.
- Enhanced Process Control: The ENTRON-EXX offers sophisticated software and hardware controls, allowing users to precisely monitor and adjust various process parameters in real-time. This level of control minimizes errors and maximizes efficiency.
- Versatile Material Compatibility: The system is designed to work with a wide range of materials, giving users flexibility in their applications. Whether depositing metals, oxides, or other compounds, the ENTRON-EXX can adapt.
- Scalability and Customization: ULVAC offers various configurations to suit specific needs, making it suitable for both research and high-volume manufacturing environments. This scalability ensures the system can adapt to evolving production demands.
- Improved Throughput: The optimized design of the ENTRON-EXX allows for faster processing times compared to older generation systems, leading to increased productivity and reduced costs.
- Reduced Downtime: The system's robust design and advanced diagnostics features minimize downtime, ensuring maximum operational efficiency.
Applications of the ENTRON-EXX
The versatility of the ENTRON-EXX makes it suitable for a broad range of applications across multiple industries. Its precision and control are particularly beneficial in:
- Advanced Semiconductor Manufacturing: Creating highly integrated circuits requires extremely precise deposition of various materials.
- High-Performance Optical Coatings: The system's precision is vital for creating optical components with superior performance characteristics.
- Next-Generation Solar Cell Production: The efficient deposition of light-absorbing materials directly impacts the efficiency of solar cells.
- High-Resolution Display Fabrication: The ENTRON-EXX contributes to the development of brighter, clearer and higher resolution displays.
Conclusion: The Future of Thin-Film Deposition
ULVAC's ENTRON-EXX deposition system represents a significant leap forward in thin-film deposition technology. Its advanced features, precision, and versatility make it an invaluable tool for researchers and manufacturers pushing the boundaries of innovation in various high-tech industries. As the demand for increasingly sophisticated devices continues to grow, the ENTRON-EXX is poised to play a crucial role in shaping the future of thin-film technology. Its precision, control, and adaptability guarantee its continued relevance in the ever-evolving landscape of advanced materials processing.
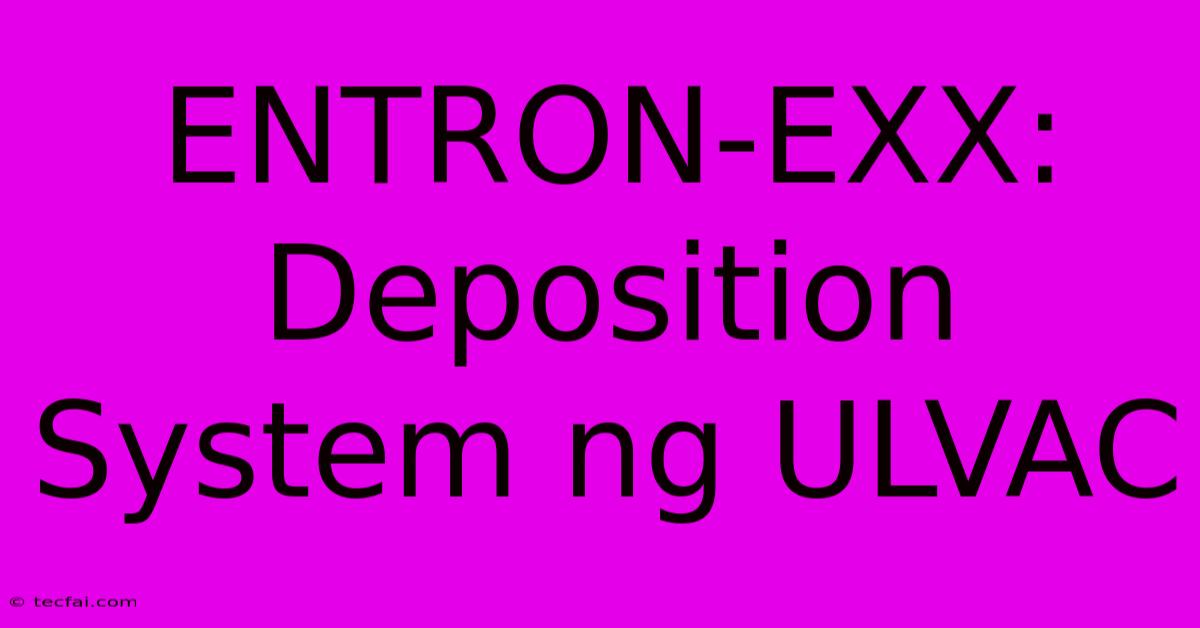
Thank you for visiting our website wich cover about ENTRON-EXX: Deposition System Ng ULVAC. We hope the information provided has been useful to you. Feel free to contact us if you have any questions or need further assistance. See you next time and dont miss to bookmark.
Featured Posts
-
Jonathan Davids Timely Hot Streak
Dec 03, 2024
-
Self Extracted Teeth Six Year Wait
Dec 03, 2024
-
Lille Stars Agent Visits San Siro
Dec 03, 2024
-
Nika Muhl Mirror Selfie Kasama Si Mad Max
Dec 03, 2024
-
Youth Services Lga Wants Ncs Funds
Dec 03, 2024